


Because these terms have exact meanings and applications, misusing them makes communicating complex ideas complicated and creating quality parts much harder to accomplish. One person’s bend allowance cannot be another person’s k-factor, and a k-factor is not a bend deduction-though I visit shops where this is precisely the case. Very few trade-specific terms are interchangeable. This statement is true whether you are learning in the classroom or discussing a project on the job. Confusion over verbiage is one of the biggest problems our industry faces. Any further guidance on this topic would be much appreciated.Īnswer: Before I delve further into this topic, I would like to begin with your comment about verbiage. Note also that this is an offset bend that will be made in a coil-fed stamping press, not a press brake, but I assume at least some of the metal forming fundamentals apply. I’m not crazy about this idea, but I think it will be OK. I was researching the topic because we are bending 0.060-in.-thick 3003 H14 aluminum (see Figure 1), and my toolmaker wants me to design the bends parallel to the grain, because the tool will be easier for him to work on. Does this mean the grain runs perpendicular or parallel to the bend line?
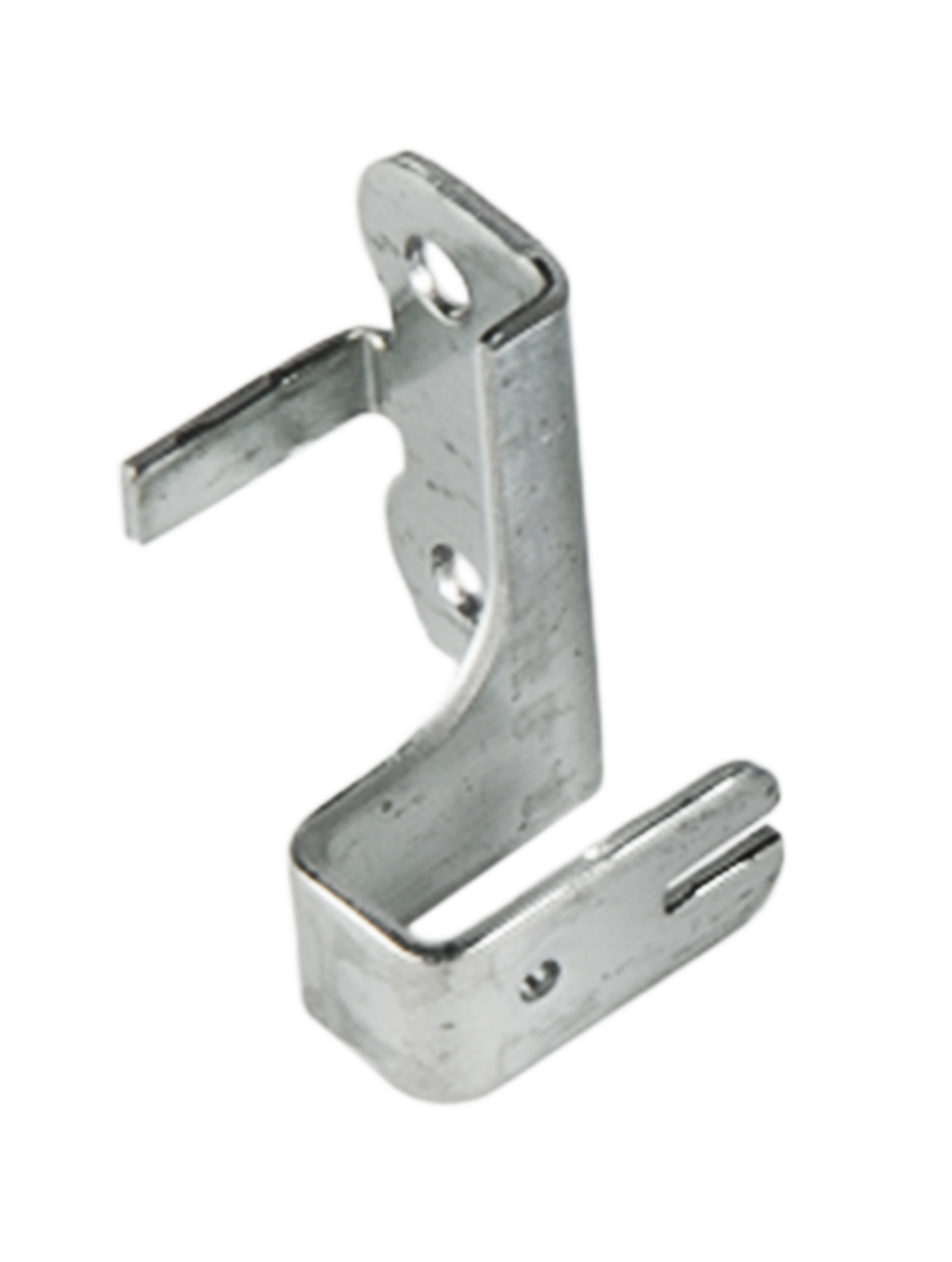
Question: A previous article of yours suggests that forming “with” the grain direction will manifest cracks. See Forging for hot metal forming operations.If press brake operators bend a small radius with the material grain-that is, the bend line runs parallel to the material grain direction, they should watch out for cracking. Stamping is usually done on cold metal sheet. Multi-step tools design and manufacturing available to achieve high speed mass production pace with the lowest unit price.Tools design and manufacturing in house.Product dimension up to Length*Width 1200*600 mm.Powder coating, galvanization, anodizing, etc Mild steel, stainless steel, aluminum, brass,etc Depending on part complexity, the number of stations in the die can be determined. Progressive dies are commonly fed from a coil of steel, coil reel for unwinding of coil to a straightener to level the coil and then into a feeder which advances the material into the press and die at a predetermined feed length. The process is usually carried out on sheet metal, but can also be used on other materials, such as polystyrene.
STAMPING STAINLESS STEEL SHEET METAL SERIES
This could be a single stage operation where every stroke of the press produces the desired form on the sheet metal part, or could occur through a series of stages. Stamping includes a variety of sheet-metal forming manufacturing processes, such as punching using a machine press or stamping press, blanking, embossing, bending, flanging, and coining. Stamping (also known as pressing) is the process of placing flat sheet metal in either blank or coil form into a stamping press where a tool and die surface forms the metal into a net shape. We have been providing thermal solutions over 10 years for almost every industrial application field covering electronics, power generations, data centers, new energy, automobile, medical, chemical and construction machinery. Custom Sheet Metal Parts Stainless Steel Stamping Parts
